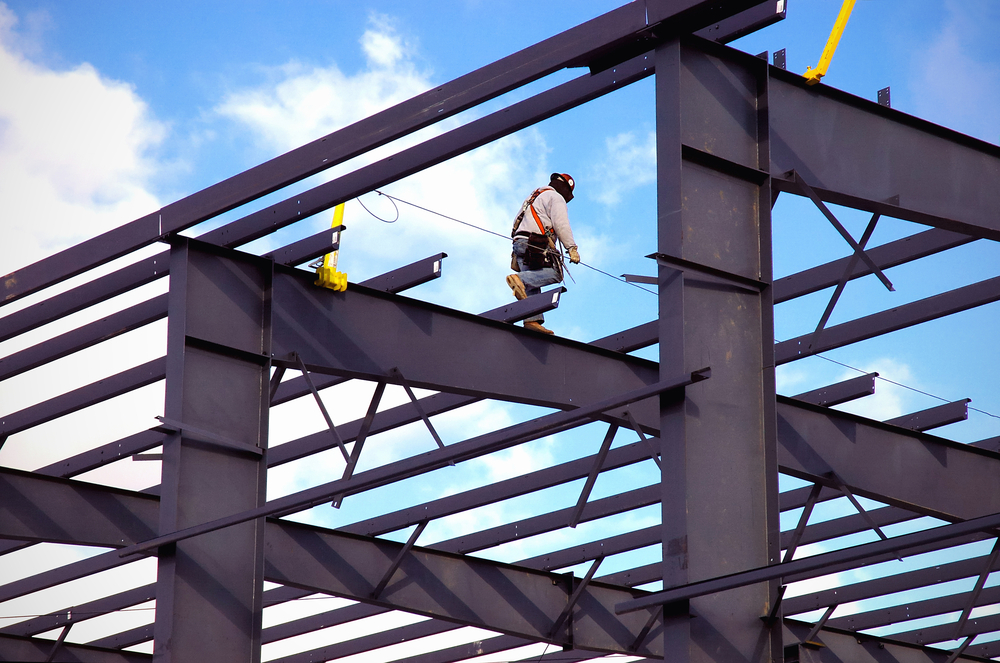
You don’t have to have traveled much in the U.S. to have heard names like the Sears Tower (now known as the Willis Tower), the Empire State Building, or the Chrysler Building. These names are as ubiquitous in America as the companies with which they are related. What they have in common is that they are all built from steel.
There is some consensus that in the U.S. the first steel building came out of the aftermath of the Great Chicago Fire of 1871. It left planners looking for solutions to the largely timber framing that destroyed thousands of buildings in the city. The result was the 10-story Home Insurance Building constructed in 1885 of a steel skeleton supported by reinforced concrete.
Since then, steel has become one of the most important and popular building products in the world. In fact, more than 50% of the world’s steel production is dedicated to the construction industry.
But Why Steel?
The use of steel ranges across a variety of industries. It’s crucial for the automotive industry, medicine, chemical and oil corporations, and for many other applications. Within the construction sector, however, all steel is not created equal. Steel known as “structural steel” is designated for use in construction.
While this may seem like a simple naming strategy, structural steel actually has very specific and rigorous criteria that must be met. But to understand that clearly, it might be helpful to first review how steel is made.
Steel is made from iron that is usually extracted (at least now) from taconite ore. Taconite is ground into a sandy composition where magnets separate out iron particles. In a process called “reduction,” carbon rich coke is combined with the iron to give the iron greater strength.
As the percentage of carbon within the mixture falls, it eventually reaches a level at which it becomes steel (less than 2.1% by weight).
Becoming Structural Steel
This newly formed steel has a high strength to weight ratio and is prized for its durability, ductility, and versatility. To become structural steel, the alloy must be further reduced to a level of between .05% and .25% carbon by weight. Not only does structural steel have to pass rigorous testing for its ability to withstand force, but it also usually takes specific forms that identify it, such as I-beams, z-shapes, tees, bars, and rods.
Structural steel is used around the world for creating building frameworks, acting as reinforcing and support rods, and as sheet products for cladding. As an added benefit, today’s steel offers 100% recyclability and has proven to be a boon to eco-concerns.
In Finland, for example, the HAMK Sheet Metal Center used steel solutions to reduce its cost of electricity and heating by over 50%. But structural steel reaches beyond the construction industry. It’s employed in crane booms, truck parts, freight cars, and transmission towers as well.
Non-Structural Steel
Not all construction-related steel is structural. Non-structural steel (essentially steel that doesn’t reach reduction levels required) is utilized for a number of construction uses. This includes heating and cooling equipment, ductwork, stairs, rails, and shelving.
Other industries thrive off of non-structural steel. The automotive industry uses stainless steel in trimwork and grills as well as exhausts systems. Furthermore, new emission reduction standards have driven carmakers to employ steel in structural components as well.
The medical sector prizes steel for its easy sterilization and its resistance to corrosion. Steel is a vital part of medical instruments, operating tables, and equipment such as MRI scanners.
In fact, you don’t have to look around much to see steel at work in the culinary industry — as part of electrical equipment, in our home appliances, and much more. So the next time you’re staring at the stunning profile of a highrise silhouetted against the sky, stop for a moment and thank steel for creating a safer, more hygienic world.